728x90
반응형
SMALL
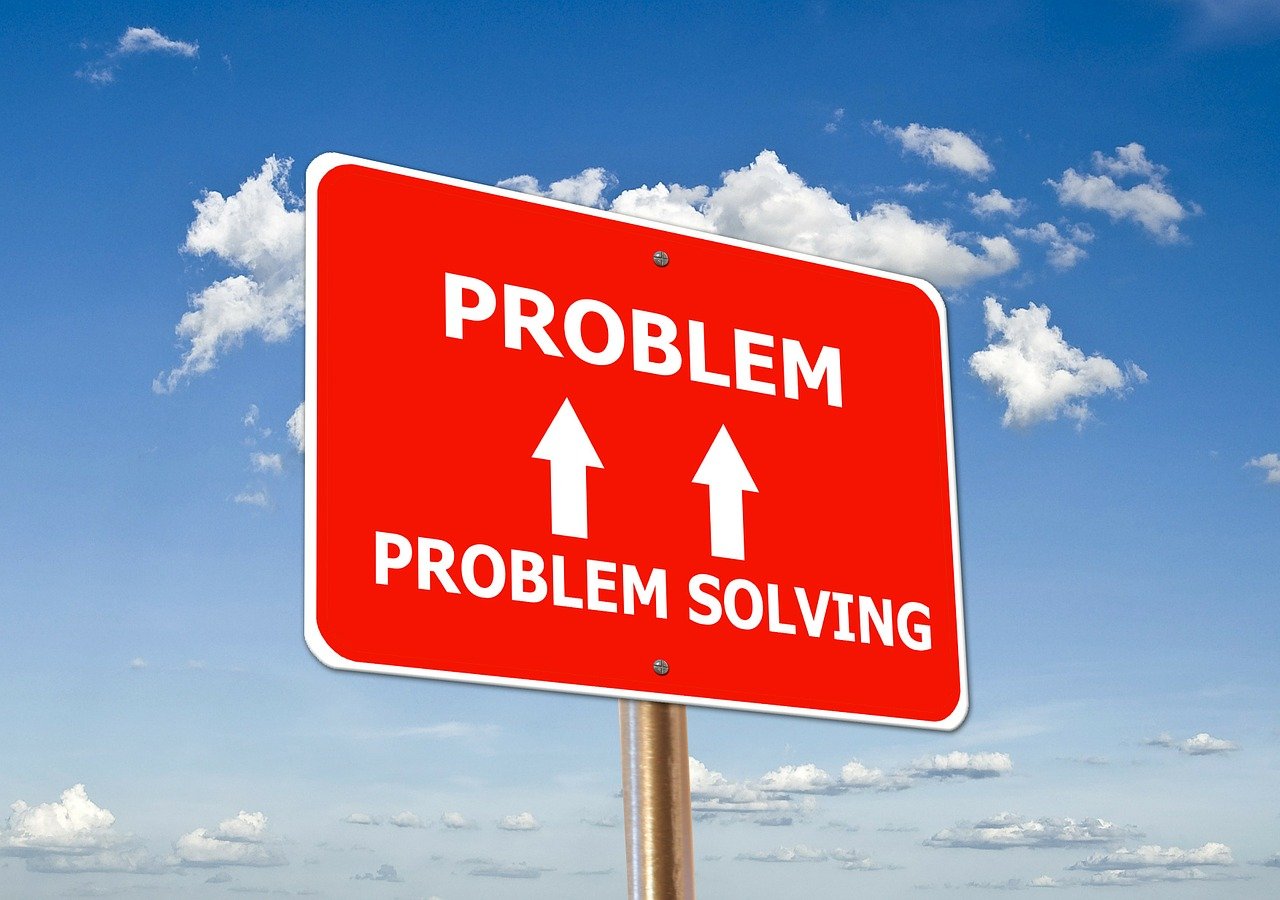
1. 문제해결 도구 - 8D
품질문제를 당면하게 되면 신속 정확한 해결방법을 요구받게 됩니다. 초기 대응은 어떻게 해야 하는지? 근본적인 원인 분석 및 대책은 어떤 방식으로 수립해야 하는지? 등 많은 경험을 가진 사람들도 문제 발생순간에 당황하는 모습들을 간간히 보게 됩니다.
이럴때 자주 사용하는 문제해결 도구가 8D입니다.
8D는 8 Discipline의 약자로, 어떠한 품질문제나 개선이 필요한 사항이 있을 경우, 8단계에 걸쳐 문제 해결하는 도구로써 하기와 같습니다.
step(단계) | 단계 내용 | 주요처리내용 | 조치일정 | |
0D | 문제의 인식 | 모든 문제를 파악하여 그 중요성 및 해결 우선 순위에 따라 문제해결 방법을 결정한다. | -.문제정리 ; 모든 문제를 파악하고 이를 정리한다. →고객불만내용, 클레임 ; 차종, 제품명, 품번외 →사내 후공정 불만, 제품, 부품 불량 -.문제해결 우선순위 결정 -.문제해결방법 결정 ; 분임조활동(영구적),TFT활동(일시적) | 1일 이내 |
1D | 팀 구성 (Establishing the team) | 해당 공정, 제품 및 개선활동 기법을 잘 알고 있으며, 개선활동에 참여할 수 있는 사람들로 팀을 구성한다. 또한 그 팀을 후원해 주는 champion을 선정한다. | -.팀 champion 또는 리더 선정 -.팀구성원 선정(4~10명정도) ; 문제와 관련된 모든 인원 참여. (사내 관련부서[품질,생산,개발,관리등], 전직원, 협력사포함) -.팀원 역할 분담 ; 관련 표준과 절차를 수정할 수 있도록 권한부여-.경영층은 팀에게 문제 해결을 위해 권한과 시간을 부여 | |
2D | 문제점 현상파악 (Problem description) | 내,외부 고객의 불만사항을 명확히 파악할 수 있도록 문제를 5W2H에 따라 계량화된 데이터 또는 용어로 나타낸다. | -.문제현상기술 ; 문제 범위와 결과, 증상 파악(고객과 협의) -.고려사항 → 고객불만을 기준으로 한 정확한 불량현상 기술 → 불량 발견장소 → 생산라인 → 고객사라인 → 필드 클레임 여부 확인 → 불량수량 -.관련 재고 파악 → 고객사 → 운송중인 출하제품 → 사내 완제품 → 사내 반제품 및 부품 →협력사 내 부품 -.타 차종 영향성 확인 ; 문제라인에서 생산한 제품 영향성 확인 -.데이터 수집 및 검토 ; 과거 및 현재의 데이터 수집 및 검토 -.문제를 세분화 -.문제 기술 ; 5W2H(who, what, when, where, why, how, how many)로 기술 -.임시(봉쇄)대책실시 및 확인 | |
3D | 임시봉쇄 조치 (Developing interim containment actions) | 영구적인 근본 대책을 실시하기 전에 문제의 영향을 내,외부 고객으로부터 격리시키기 위해 임시(봉쇄)대책을 실시하고, 그 효과를 확인한다. | -.임시대책 여부 결정,임시대책안 수립, 최적 임시대책 선정 → 문제가 더 이상 고객(사내,사외)에게 발생되지 않도록 즉각적인 조치가 취해져야 함. → 잠재적인 위험검토 ; 이미 고객에게 인도되어진 제품에 대해 향후 발생될 위험에 대해 검토 → 생산되는 제품검증 확인(동일불량 포함여부) → 고객과의 조율을 통해 고객 승인을 득해야 함. -.중요점검사항 → 선별된 양품 식별 → 수행된 조치의 유효성 검증 → 잠재적인 부정적 측면 영향 검토 → 고객재고 > 운송중 재고(포장사 재고포함) > 사내 완성품재고 > 사내 반제품재고 > 사내부품재고 > 협력사부품 순으로 봉쇄조치 실시 ★봉쇄조치 실패는 고객에 동일불량을 지속적으로 발생시키게 됨으로 반드시 위 순서로 누락되지 않게 봉쇄해야함. | |
4D | 근본원인분석 (Root cause analysis) | "왜 문제가 발생하였는가?"를 설명할 수 있는 모든 잠재원인을 조사하여 분석,검증하고, 근본원인을 찾아 대책을 선정한다. | -.잠재원인조사 및 분석 ; 발생원인, 유출원인, 시스템 원인을 조사한다. →가능한 원인 인자 도출을 위한 표준화된 품질기법 적용 ; FTA분석(4M기준), 5WHY, FMEA → 문제가 발생할 수 있는 모든 원인을 나열하여 분석 → 원인들에 대해 가장 빠른 방법, 저비용 등의 검증방법 선택 → 고객의 불만 내용을 사내의 기술적 문제로 파악 → 원인과 결과 관계 명확(브레인스토밍법) → "무엇이, 언제" 변화되었는가? → 문제 기술 내용에 대한 비교분석 -.고객불만 및 필드클레임에 대해, 특히 NFT(원인불명)의 경우, 협력사는 보다 체계적으로 분석하여야 함. | 7일 이내 영구조치 또는 품질문제 사안에 따라 일정이 더 당겨질 수 있음. |
5D | 영구대책 시행 (Permanent corrective action) | 선정된 대책이 그 문제 해결은 물론 다른 문제를 일으키지 않는다는 것을 통게적인 방법으로 확인한다. 필요시 예상되는 문제에 대한 조치들을 마련한다. | -.원인에 대한 대책을 수립한다. ; 발생대책, 유출대책, 시스템 대책을 수립한다. → 완료예정일, 책임자, 담당자를 지정하여 항목별 개선을 진행. -.수립된 대책안 검증을 실시한다. → FMEA실시 → Pilot test를 진행하고, 모니터링 한다. ★결정된 근본원인의 재발을 확실하게 방지하기 위해서는 Error Proof대책을 수립한다. | |
6D | 근본대책의 유효성 확인 (Validate permanent corrective action) | 영구적인 근본대책을 마련하여 실시한다. 근본원인 제거 확인을 위한 관리방법 및 지속적인 모니터링을 실시하고, 그 효과를 파악한다. | -.필요시 영구 개선대책 적용을 위한 추가팀 구성 -.Champion은 영구 개선대책 승인 및 적용 책임 -.영구 개선대책 적용을 위한 실행계획 작성(P-D-C-A) -.FMEA 재검토 및 유효성 모니터링 →품질특성에 대한 Cpk, 불량율(ppm) →현상과 비교 개선 효과를 30일 이상 데이터로 제시 ★ 만약 개선대책의 유효성이 확인되지 않는다면 근본원인이 명확하게 파악되고, 영구대책이 수립되기 전까지 봉쇄조치를 지속적으로 시행해야 한다. | |
7D | 재발방지대책 (Preventive action) | 문제의 재발과 모든 유사 문제들을 예방하기 위해 관리체계의 표준을 정비하고, 관련부서에 통보한다. | -.재발 방지를 위하여 3D~6D 단계 지식 및 정보를 활용한다. -.제품과 공정에 관련된 표준문서를 개정조치한다. ; DFMEA, PFMEA, 관리계획서, 작업표준서, 자주검사 체크시트, 설비일상점검표등 -.관련부서 교육실시. -.유사제품, 공정에 수평전개를 실시한다. -.대책에 대한 주기적인 audit를 실시한다. | |
8D | 보고 및 활동평가 (Team &individual recognition) | 활동결과에 대한 문서화와 보고화 등을 통해 수평전개 활동을 실시한다. 문제 해결에 기여한 팀원 또는 참여한 인원들에 대한 격려와 활동 결과를 인정한다. | -.개선활동 완료여부 검토 및 최종 8D Report를 작성하여 고객승인을 받는다. → 필요시 고객사 방문하여 개선대책을 발표하고, 추가 고객 요구사항 발생시 검토 및 적용한다. -.팀과 개인의 노고와 공헌을 인증(필요시 성과에 따라 incentive부여) -.Team champion은 팀과 개인포상 |
728x90
반응형
LIST
'품질이야기' 카테고리의 다른 글
Re-start Checklist - 생산 가동 전, 후에 대한 점검사항들 (0) | 2024.10.02 |
---|---|
품질비용(Cost of Quality) : Q-Cost (0) | 2024.08.20 |
IATF 16949 내부심사 정의, 목적, 형식, 분류등 (0) | 2024.08.12 |
측정실 환경관리, 길이 분야 측정실 환경기준 (1) | 2024.04.03 |
주요성과지표 KPI(Key Performance Indicator)의 개념 및 지표관리 (0) | 2024.04.02 |